Reading Time: 8 minutesThis article was published on Mar 2014 in Building Review Journal Vol 29 No. 2.
Text by Delene Lee, Images by Tekla.
Over the past 5 years, Asia Pacific has become the largest market for the concrete and cement industry, accounting for 58.1% of the global market. Developing economies in the region, especially China, India and Indonesia, are expected to support the expansion of the concrete and cement markets, due to the rapid development of infrastructure and an increase in residential construction.
With such a large and competitive market, contractors and engineers are on a never-ending quest to save time, reduce waste, and ultimately cut down costs.
How can BIM help these companies to reach those goals?
Today, architects and builders are increasingly embracing the benefits of BIM. The days of old-fashioned computer-aided design (CAD) and marked-up drawings are numbered. The future of construction is with BIM.
Unlike plain-vanilla CAD, BIM software creates a three-dimensional (3D) model full of smart objects embedded with information. BIM makes it easier to integrate architecture with engineering work, avoid “clashes” of building elements, instantly output lists of materials and labour, and automate valuable tasks like simulating the effects of sunlight in an interior space. With such details, BIM ultimately cuts down on rework and errors on site, leading to lower costs.
In a recent exclusive interview with Mr. Andy Dickey, he shed some light on how BIM helps the various stakeholders in the construction value chain and justifies the common barriers of adopting BIM. He also shares about a BIM software that one can download and use for coordination and communication on a project – for free, which is great for those who have yet to experience what BIM has to offer.
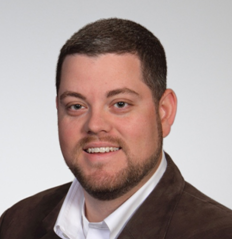
Mr Andy Dickey
Business Development Manager
Tekla Corporation
Andy is currently the CIP Concrete Business Development Manager for Tekla, a Trimble Company, based in Espoo, Finland. With extensive experience in the cast-in-place concrete industry, he now focuses on delivering BIM (Building Information Modeling) solutions for use in all phases of CIP Concrete Construction to Tekla Corporation customers worldwide.
BRJ: Who should adopt BIM Technology?
AD: We have quite a lot of stakeholders in the construction industry, but it is mainly these four categories of people: architects, engineers, contractors and owners (A,E,C,O). Tekla is particularly focused on engineers and construction professionals.
BRJ: What are the benefits that BIM deliver at every stage of the construction process?
AD: I think one of the biggest problems over the years has been productivity. One of the leading causes for that is really bad information… also known as drawings. So, BIM is a vehicle for a superior way to communicate amongst all the projects stakeholders; as communication and information can really affect productivity greatly. Particularly important in a market like Singapore, similar to the States, which has quite a lot of international workers in the construction field, and 3D is really a superior way to communicate with people that speak different languages.
BRJ: How can BIM make an impact in the Asia Pacific construction sector?
AD: One of the most prevalent forms of construction in Asia Pacific is reinforced concrete. Tekla is quite strong in providing BIM tools in this area. It is traditionally something that is very difficult to coordinate between various disciplines like mechanical electrical plumbing, fire protection, including all the reinforcing. As that part of BIM is growing, I think that particularly helps the Asia Pacific region because the reinforced concrete material type is so prominent.
BRJ: How is Tekla’s BIM solution different from its competitors’?
AD: I would say the primary difference is the fact that we offer solutions end to end. What you tend to see are tools that focuses on either design or pre-construction, or construction. But, Tekla is really in the verticals that we occupy – which is structural steel, precast concrete, reinforced concrete, we offer the solution end to end.
One of the reasons why productivity is so bad is because you are passing drawings downstream at every one of those stages that I’ve mentioned – from design all the way to construction. With Tekla, you can pass a model, so you don’t have this loss of information. You are not passing bad information from one stage to the next; you are passing really good information in Tekla, all the way through the process. That is what makes us different. We can tie the process together end to end, digitally.
BRJ: Does it require the all the various stakeholders to be trained in BIM technology to be able to work cohesively on a project?
AD: Yes, but the training you receive as construction engineers is quite different from a site supervisor, so it really needs to be tailored to the way in which they are using the software. And that is one of the things that we did. Engineers are learning about our analysis in design capability, while the site supervisors are probably not – they are just learning how to pull out quantities for how much concrete they need to order.
We configure different interfaces to match different needs of the various stakeholders – such that they don’t see certain buttons that they don’t need. It avoids confusion. The training is compartmentalised as well and that really helps make it easy. Even if they are just using models in a basic way, they can still work effectively.
BRJ: There are costs and required BIM-related training involved that can deter some companies from going forth to adopt this technology. What advice would you give to them?
AD: That’s a challenge in many markets and capital expenditure is always a concern, especially what we have been through the last few years of the economy slowing down. Now, with the economy speeding up, it has a new set of challenges – cash flow is an issue. They have to know that the return on investment (ROI) is definitely there. And it is a very quick ROI. If they don’t allocate the capital expenditure, they put themselves at risk going forward, as their competitors are doing that and significantly lowering their costs.
The cost of the software is actually the lowest amount of money that they are going to spend. Companies spend the most of their money on the people; training employees (which extends beyond BIM-related training), paying their hours etc. Hence, a small investment tool like Tekla is a small price to pay to magnify the productivity of the human capital. It can really multiply the effectiveness of that person.
BRJ: You mentioned a very quick ROI…do you have any examples to justify how long the payback is, in financial terms?
AD: We don’t reveal those statistics as it is difficult to be really specific about it. However, based on the feedbacks from our customers, they are telling us that it is very quick. You could check out some of our case studies, it is very detailed on what they did and how they implemented the software as well.
(Editor’s note: Those case studies found on http://www.Tekla.com/references)
BRJ: Is BIM technology appropriate for retrofit projects?
AD: Definitely! It is appropriate for renovations, retrofits, and additions. Tekla is a trimble company, which does so many things. But one worth noting is the positioning technologies. You could actually find out the position of the existing structure or elements and bring that information back into Tekla. The result of that is one of two things – with the total station you get the centre points and with the laser scanner you get a 3D model. You can bring either one of that into the Tekla environment and model the new stuff relative to where the old stuff is.
We get a lot of feedback – we have a case study coming out later in the year, a customer in the States, doing a project on a senior-living facility. They built drawings instead of using the drawings that they got from the City. Those drawings didn’t match where the existing building was supposed to be. But they were able to use the tools to properly locate it and accuracy became a non-issue.
BRJ: Are there any current key events or factors that would drive the adoption of BIM technology in the Asia Pacific region?
AD: They are the ones that I have already mentioned – communicating across quality information, overcoming language barriers, and productivity. Productivity is always a concern. Especially when you have hyper-growth rates that you see in some of the markets in Asia Pacific, it is a way to better manage that growth with a limited supply of resources. In some markets, labour is cheaper than the others, but good labour is always a limited supply at any price. The models can really enable quality work at almost any experienced level.
BRJ: What are your thoughts on future technology and trends predicted with BIM?
AD: It is all up from here – BIM for construction is probably the biggest growth area – particularly, in the area of connecting from design and detailing to the construction site.
A lot of what the designers BIM would be conceptual, because it’s to the level of detail that they need. But with Tekla, you get all the construction level of detail – every piece of reinforcing bar, cast, and all other tiny details on a project wide basis. You end up with a really detailed model but having the tools to make sure it really happens that way in reality – connecting the reinforcing bar information in the model to the machine that makes it, or connecting the position of things in the model to the robotic total station out on the site –that’s the next big thing and that’s the area that we are really strong in and heavily investing in.
BRJ: Is BIM stable at the moment or is it still developing?
AD: Its stable, but whenever you develop something, people want more. We see all sorts of ways to improve all the time as we engage with our customers. They provide us the shining light to see where to go to next.
BRJ: Do you have anything else you would like to share?
AD: Tekla has two main product lines – Tekla Structures it’s a tool you pay if you are in any of those interest groups that we were discussing, we also have Tekla BIMsight which is a free BIM tool that anybody can download and use and it’s a professional grade and I would recommend for anybody to download it and try it out.
BRJ: How long is it free for?
AD: Forever! Doesn’t mean it won’t change (eg. adding things to it). Our intention is to keep it free. It is a coordination tool, you can mark up, and it comes with a sample project. I really strongly encourage it to those interested in BIM and who doesn’t want to run out and spend a whole lot of money tomorrow or maybe next week right? (laughs)
BRJ: So then people won’t have to purchase BIM software anymore?
AD: Well…it addresses a few workflows, but you cannot make models with it. It is just to give people a taste on what they can do and what to expect. If they are already heavily involved in BIM, it is also a tool they can use for coordination and communicating on a project. The website is Teklabimsight.com, if anyone wants to check that out!
AD: Another thing I would like to add is that continuing to work in 2D drawings is the root cause of the lack of productivity. We really won’t see the productivity curving up until we move away from drawings as being is the only source of information on the project.
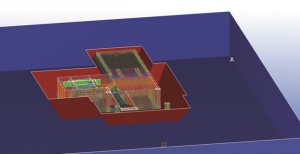