New Dedicated Solutions For Construction
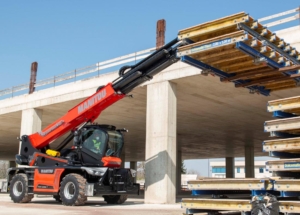
MRT2260
- Complete overhaul and extension of the Manitou range of rotating telehandlers
- Three new segments: compact fixed telehandlers, ultra-compact telehandlers and articulated loaders
- Even lower Total Cost of Ownership
Manitou Group, the worlwide reference in rough-terrain handling, aerial work platforms and earthmoving, has unveiled the new segments in its construction range with new compact fixed and ultra-compact telehandlers, as well as new articulated loaders. The group also ushered in a complete overhaul and extension of its range of rotating telehandlers at the digital “BUILD THE FUTURE” event broadcast worldwide.
In order to offer a unique, 100% digital launch, Manitou Group organized the “BUILD THE FUTURE” event. Accessible via an interactive platform, the event brought together more than 3,000 internet users in 90 countries across 4 continents, including many dealers, rentals, key accounts and media. Over the course of two days, visitors were able to remotely discover, through a talk show, three new segments in the construction and MRT rotating telehandler range, followed by workshops showcasing the group’s commitment to supplying comprehensive and durable solutions.
Fully redesigned MRT rotating telehandlers
To bring clarity to its range of rotating telehandlers, the group has decided to rename its two ranges under the new names VISION and VISION+. Carlo Alberto Razzoli, MRT Product Manager, explains this change: “We are seeking to harmonize our entire range by making it simpler. By modernizing the design and ergonomics of our products, we are now able to offer a single cab across all the models in the range, thus providing excellent visibility to users whatever the model. Having the same cab also means having an equivalent control station on all models, making them quicker to get to grips with”.
Two new machines have been added to this offering with the MRT 1645 and MRT 1845 models for the VISION range. With 500 kg (1,100 lbs) of additional load capacity compared to their predecessors, these two products offer a lifting height of 16 meters (52’5”) and 18 meters (59’1”) respectively for a load of 4.5 tons (9,900 lbs). They are also equipped with a new Stage V engine, producing power of 75 hp and 116 hp respectively. The VISION range offers a wide selection of 14 models with heights ranging from 16 meters (52’5”) to 25 meters (82’), for a load capacity of up to 4.5 tons (9,900 lbs).
The highest capacities are grouped together in the VISION+ range, which features 12 new models. The range has been completely revamped with six new products: MRT 2260, MRT 2660, MRT 3570 (also available in an electronic suspension version), MRT 2570 and MRT 3060. Carlo Alberto Razzoli explains the reasons behind the renewal of the range: “There is growing demand from customers wanting machines that offer higher performance on construction sites. This high-capacity range meets these expectations perfectly with a very high level of equipment”. With models offering a lifting height of 22 meters (72’9”) to 35 meters (114’8”) and a much improved capacity of up to 7 tons (15,400 lbs), this range is ideal for the installation of structural steelwork, renovation of buildings and even demolition. These two ranges are connected as standard in order to optimize maintenance, increase the machine’s operating hours and therefore reduce the total cost of ownership for the user. The VISION and VISION+ ranges are now available worldwide and will be delivered to the dealer network, to rentals and to key accounts by September 2021.