Reading Time: 5 minutesBuildings are valuable assets but the costs of maintenance can affect the bottom line of a business. As energy
costs continue to rise, building owners and facility managers face increasing pressure to reduce operational
costs, at the same time, increase productivity, improve sustainability and ensure business continuity for their
organizations.
A building’s chiller plants typically consume the most energy, so it makes sense that any strategy to reduce costs and to be environmentally friendly needs to start here. Johnson Controls is a global multi-industrial company with established core businesses in the building and automotive industries. It leverages on decades of YORK chiller innovations to deliver more efficient and sustainable chiller solutions in its continual push of the boundaries of chiller technology.
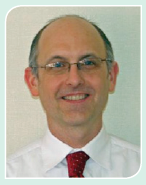
Larry Kouma
Product Management Director,
Asia Chiller Solutions, Johnson Controls Inc.
With over 20 years of experience in the HVAC industry, Larry boasts
vast technical knowledge in the design and application of steam and
chilled water systems. He is passionate about driving sustainability
across the value chain and has spent over a decade working with
energy efficiency standards. In addition, he has served on the
ASHRAE-ANSI 90.1 Standard Committee for 8 years.
In a recent interview, Mr. Larry Kouma (Product Management Director) shared his insights into regional trends in Asia’s refrigerant industry and on how the YORK® Magnetic Centrifugal Chiller (YMC2) system addressed the most pressing concerns of facility owners and designers.
BRJ: What are the regional trends in the refrigerant industry in 2014?
LK: With the awareness of ozone depletion and commitment to the Montreal Protocol, major suppliers are responding to the phase out of hydrochlorofluorocarbons (HCFCs). However, meeting all the requirements of safety, reliability, efficiency, Ozone Depleting Potential (ODP) and Global Warming Potential (GWP) is a tall order. The refrigerant that best fulfils these requirements are the hydrofluorocarbons (HFC) for large HVAC equipment applications, and in certain applications, natural refrigerants including hydrocarbons, ammonia, and carbon dioxide (CO2), are also safely applied.
BRJ: In what direction would these trends change in the next few years?
LK: Increasingly, refrigerants are also assessed based on their Life Cycle Climate Performance (LCCP), which takes a holistic approach in estimating all warming impacts – both direct and indirect – over the lifetime of the refrigerant for specific applications. Research will continue to push forward to find or create refrigerants that best fulfil all the necessary criteria while minimizing climate impact. Meanwhile, HFCs look to be the mainstay with European Union F-Gas Regulation to mitigate its GWP by addressing the containment, use, recovery, reporting, labelling, training, certification and some market prohibitions. This will have implications especially for sectors with high leakage such as automotive and commercial refrigeration.
BRJ: What are some of the most pressing building and facility challenges faced in the industry today?
LK: Rising energy costs and the need to improve productivity and minimize downtime continue to be key challenges for building and facility managers today. In addition, there is growing interest in sustainability across the industry as organizations increasingly seek to incorporate it into business goals and culture.
With the increased focus on climate change globally, many countries are enacting legislation and providing
incentives to modernize and retrofit existing facilities. In fact, the recent 2013 Energy Efficiency Indicator (EEI)
study by Johnson Controls found that such government policies and programs were one of the key drivers for
Asia to adopt “greener” and more energy efficient HVAC equipment and solutions.
In Singapore, the government’s push to green 80 percent of all buildings by 2030, mean that building owners
and facility managers will increasingly look to proven and reliable HVAC and solutions to help them to achieve
their energy efficiency and green building targets in the next few years.
BRJ: How does YMC2 help address them?
LK: Johnson Controls is one of the first to apply the magnetic-bearing technology to chillers, originally in response to mission-critical needs of the navy. Subsequently, we then extended this technology to make it available to other sectors (including commercial) to help address the growing demands with energy consumption reductions and sustainability. The magnetic-bearings reduce friction and vibration, while eliminating the need for oil to lubricate the bearings – delivering energy-efficiency, high reliability and noise control as a result. It addresses these challenges through:
Improved Efficiency – YMC2 chillers is 10 percent more efficient than new conventional, variable-speed chillers. The magnetic-bearing technology eliminates mechanical-contact losses in the driveline. In addition, proven energy efficient YORK® features such as the OptiSpeed™ variable-speed drive and the optimized centrifugal compressor have been retained and improved on. The efficiency benefits can be greater than 30 percent when considering replacement of an older existing chiller at end of life.
Reduced Noise – The YMC2 chiller is quieter than any water-cooled centrifugal or screw chiller on the market. Driveline vibration is eliminated with the magnetic-bearing technology, while the YORK® OptiSound™ control further helps reduce noise. As a result, the YMC2 chiller operates at a maximum of 73 dBA at full-load standard conditions (The human ear would perceive the YMC² chiller only half as loud as other magnetic-bearing chillers).
High Reliability – The design of the YMC2 chiller has fewer moving parts, requires less servicing and has a longer motor life. This helps to increase reliability and reduce maintenance costs. The chiller’s permanent-magnet motor has an inherently longer life than traditional motors, and the OptiSpeed drive’s soft-start sequence helps to further extend motor life.
Better Sustainability – The YMC2 chiller uses refri-gerant HFC-134a which has zero ozone-depletion potential. Furthermore, it is designed with 57 percent less refrigerant-piping connections which drastically reduce the potential for direct global warming caused by refrigerant leakage potential. The 10 percent to 50 percent efficiency improvement also reduces indirect global warming caused by greenhouse-gas emissions generated by electric utilities. Indirect impact is typically more than 95 percent of the chiller contribution to environmental warming impact over the operating life of the chiller.
BRJ: What is the potential for adoption of the new YMC2 technology in Asia?
LK: We see lots of potential for adoption in both the developed and developing markets in Asia. Interest in the developed markets, such as Australia, Hong Kong and Singapore, would be more immediate and widespread. For one, the YMC2 chiller is ideal for retrofit installations because it not only delivers higher efficiency but also caters to a higher capacity within a small footprint.
We are also starting to see interest in developing markets, such as India and China, where a few forward thinking companies have started to implement high efficient systems and solutions. At the same time, the governments in these countries have increasingly taken steps to drive the adoption of more energy efficient and green solutions across businesses and infrastructure through regulations and incentives. So we can expect good growth in these markets in the coming years.
In general, YMC2 is a versatile solution that is suitable for application across a wide range of industries. Given its high reliability and superior sound control, it is also recommended for high performance facilities such as data centers, healthcare facilities, educational institutions and concert halls.
BRJ: In terms of cost savings, how long is the payback with YMC2 installed?
LK: Generally less than five years, and can be lower than three years depending on total system design and ambient conditions.
BRJ: Does YMC2 help existing buildings? Please elaborate.
LK: The YMC2 contributes towards helping reduce the energy consumption and operational costs of commercial and industrial buildings. It is also ideal for retrofit in existing buildings because of its small footprint – it can fit into the old chiller space and still cater to a higher capacity (up to 560TR) and deliver higher efficiency. Its energy efficient and sustainable features also help existing buildings meet the energy management and environmental targets set out by building owners and increasingly, governments.
In Singapore, government legislation and incentives play a big part in driving the adoption of more energy efficient HVAC solutions. This is in part due to the Government’s push to green 80 percent of all buildings by 2030.
New regulations increasingly require new and existing buildings to achieve a minimum Green Mark standard when retrofitting or installing a new cooling system. Existing buildings are also required to carry out regular energy audits and report annual energy consumption data.
Johnson Controls, has helped existing buildings such as PoMo, a mixed-use retail facility achieve the BCA Green Mark Platinum rating with YMC2. The YMC2 helped address the needs of the building owners by reducing energy consumption and controlling excessive equipment noise. With the YMC2, the retrofitted chiller plant achieved an impressive system efficiency of 0.65 kW/RT and successfully lowered sound levels below 73 dBA.