Reading Time: 6 minutesIdo Eylon is the General Manager of Asia South, Stratasys Inc., he is responsible for the overall operation of the business while ensuring sustainable growth of the 3D printing business across Australia, Southeast Asia and India.
Ido started his career at Stratasys as an Applications Engineer in the company’s headquarters in Rehovot, Israel. He has gained extensive experience with the company’s technology and its applications across various industries and has collaborated with many of Stratasys’ customers from diverse trades. Ido has also assisted in a variety of projects to further expand and implement the applications and use of Stratasys products in numerous areas. By taking part in these activities, Ido contributed to discovering new and innovative solutions for Stratasys products. He has also been invited to speak at many events to spread and share his in-depth experiences.
Ido holds a Biomedical Engineering degree in Ben Gurion University.
At a recent launch of Stratasys’ new 3D Printing Experience Centre, Building Review Journal had an exclusive interview with Ido, to share more about how 3D printing can impact the architecture industry.
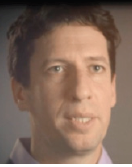
Ido Eylon
General Manager,
Asia South Stratasys AP Ltd.
BRJ: How have Stratasys’ customers in the architecture industry in the region and other parts of the world benefited from 3D printing?
Ido Eylon: Architectural bureaus can save a significant amount of time because 3D printers can achieve the characteristics of a model much faster, especially when complex geometries are in question. Architects can also easily validate designs and make good decisions earlier before committing to a final model because of the product realism. With the latest Connex3 released earlier this year, Architectural bureaus benefit from color printing and more productive and efficient printing processes with three different base materials ready-to-print on a single job.
The following are case studies that showcase the value of 3D printing to the architecture industry:
1) Seoul, Korea: Modelzium Architectural Modeling Firm Enhances Competitiveness with Objet 3D Printer Modelzium purchased the Stratasys Objet Eden350TM 3D Printer and were impressed by the fine details and smooth surface finish of the printed models. Compared to the previous CNC and manual method, by using 3D printing technology model turnaround time has been reduced by 30 percent for simpler designs and 50 percent for more complex designs. Another benefit Modelzium mentioned was that by using 3D printers to produce architectural models, they were able to cut production cost by 30 to 50 percent.
2) Toronto, Canada: McCann Architecture Architectural Modeling Firm Builds Scale Model of
Stunning Abu Dhabi Edifice with 3D Printing. Peter McCann Architectural Models Inc. (PMAMI) uses Stratasys 3D printers in order to be able to provide their customers the best architectural models possible. One of their clients was Chicago-based Smith+Gill Architects for whom they created a large model of Masdar Headquarters, the world’s first large-scale positive-energy building that generates more energy than it consumes. Stratasys 3D printers helped Smith+Gill to print a model that included multiple helix-shapes that needed to be both precise and strong because they were structural. Without the printer it would not have been possible for them to build the free-flowing roof for the Masdar HG model.
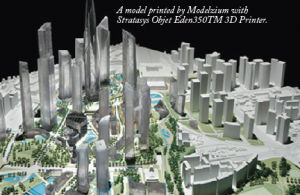
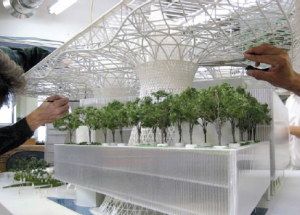
A model of Masdar Headquarters printed by Smith+Gill Architects using Stratasys 3D printing technology.
BRJ: What is Stratasys’ vision for the new Demo Centre in Singapore and the value it brings to customers/prospects in the region?
Ido Eylon: As a leading 3D printing industry player, Stratasys recognises the importance of implementing a global strategy in local context. Establishing a 3D Printing Experience Centre in Singapore allows our customers to see our innovative technologies in action and realise the values and advantages of 3D printing technology. A local demo center allows us to provide local support and offer accessible 3D printing solutions to serve the growing needs in South Asia and Pacific region. The establishment is also well aligned with our corporate vision to make 3D printing more accessible and to help customers revolutionise their product design and manufacturing processes. The demo center showcases the full technology portfolio ranging from desktop 3D printers to large, advanced 3D production systems, thus enabling designers and engineers to create models and prototypes for new product design and testing and to build finished goods in low volume.
While Asia-Pacific is the fastest growth engine of the Stratasys, contributing 21% of the company’s revenue (as at Q2 2014), Stratasys is committed to continuing its investment in the region to sustain the momentum.
The company has over 2,500 employees globally with approx. 200 based in Asia. Stratasys has a strong local presence in Asia with 8 offices in the region. Stratasys is confident about the future growth of the 3D printing market in Asia and continues to invest in strengthening its sales, marketing and channel infrastructure in the region and globally.
BRJ: What materials can 3D printing produce?
Ido Eylon: Stratasys offers a range of additive manufacturing materials, including clear, rubberlike and biocompatible photopolymers, and tough high-performance thermoplastics. This variety lets users maximize the benefits of 3D printing throughout their product-development cycle.
Two leading 3D printing technologies including:
Fused Deposition Modeling (FDM) Technology works with production-grade thermoplastics to build tough, durable parts that are accurate, repeatable and stable over time.
PolyJet Photopolymers offer fine detail along with final-product realism surpassing all other 3D printing technologies. They exhibit a chameleon-like ability to simulate clear, flexible and rigid materials and engineering plastics — and even combine many colors and material properties into one model.
BRJ: Stratasys recently launched a new product, can you share more about that?
Ido Eylon: Yes. In February this year, Stratasys launched the latest printer, the Objet500 Connex3 printer which enables an incomparable product realism and enhanced functionality with the revolutionary three-base-material capability.
The printer features a unique triple-jetting technology that combines droplets of three base materials to produce parts with virtually unlimited combinations of rigid, flexible, and transparent color materials as well as color digital materials – all in a single print run.
The Objet500 Connex3 lets users build rigid, rubber-like and clear parts into one model and offers hundreds of composite materials, blended right in the 3D printer. There are three color base materials – VeroCyan, VeroMagenta and VeroYellow – which are combined to produce hundreds of vivid colours. It eliminates secondary operations, such as assembly and painting. And when combined with Stratasys’ extensive range of PolyJet photopolymer materials including digital materials, rigid, rubber-like, transparent, and high temperature materials, Connex3 helps users to produce prototypes which simulate standard and high temperature engineering plastics.
Connex3 can simultaneously build as many as 46 hues/ material characteristics into an individual part, assembly or multi-part job in a single process.
BRJ: How is 3D printing different from the traditional modelling methods?
Ido Eylon: 3D printing is complementary to traditional manufacturing methods and benefits the users in many ways such as:
Shorter Time-to-Market: Users can print an assembled part without assembly or painting which is a significant time-saver. It helps architectural bureaus to validate designs and make good decisions earlier before committing to building.
Minimize costs-of-errors: prototypes can be created in a cost-effectively manner, allowing design reiterations prior to project initiation.
Confidentiality: Having an in-house 3D printing system would minimize the risk of design leakage.
Liberate Creativity: The ability to print complex geometries, and even more so with three different base materials simultaneously expands both the number of materials available and the number of combinations in an individual part. With a wide range of advanced material option and dozens of composites, user’s designs will come to life as realistic models, with materials characteristics like colours, rubber-like and transparency, earlier in the design process.
Optimized model development process: Stratasys printers enable to print out models that look like the final building. Fine feature quality provides high detail and smooth surfaces to create brilliant, precise 3D models. The product realism enables designers to build models with final product quality, not only to impress the audience in a pitch, it also helps to eliminate costly design errors at early stage of the model development process.