Opening of Peljesac bridge
MCI® Technology Applied on One of the World’s Most Demanding Construction Projects!
On 26 of July, Pelješac Bridge, the largest ever EU infrastructure investment in Croatia, officially opened in grand ceremony. The bridge, providing a road link between two parts of the country is of strategic importance and is one of the most substantial EU infrastructural investments ever. It connects the region of Southern Dalmatia with the rest of the country’s mainland. The bridge will cut travel time by 37 minutes along the Adriatic coastline, improving people’s lives and increasing economic opportunities for the region. It has 13 spans, five of which are 285 meters long, six centrally placed reinforced concrete pylons with a height of 33 meters, and two lanes together with a stop lane that will serve for bridge maintenance.
Peljesac bridge is ranking among the most demanding bridges in the world—in complexity of construction and design. Bridge is 2,404-m (7,887.14-ft) long.
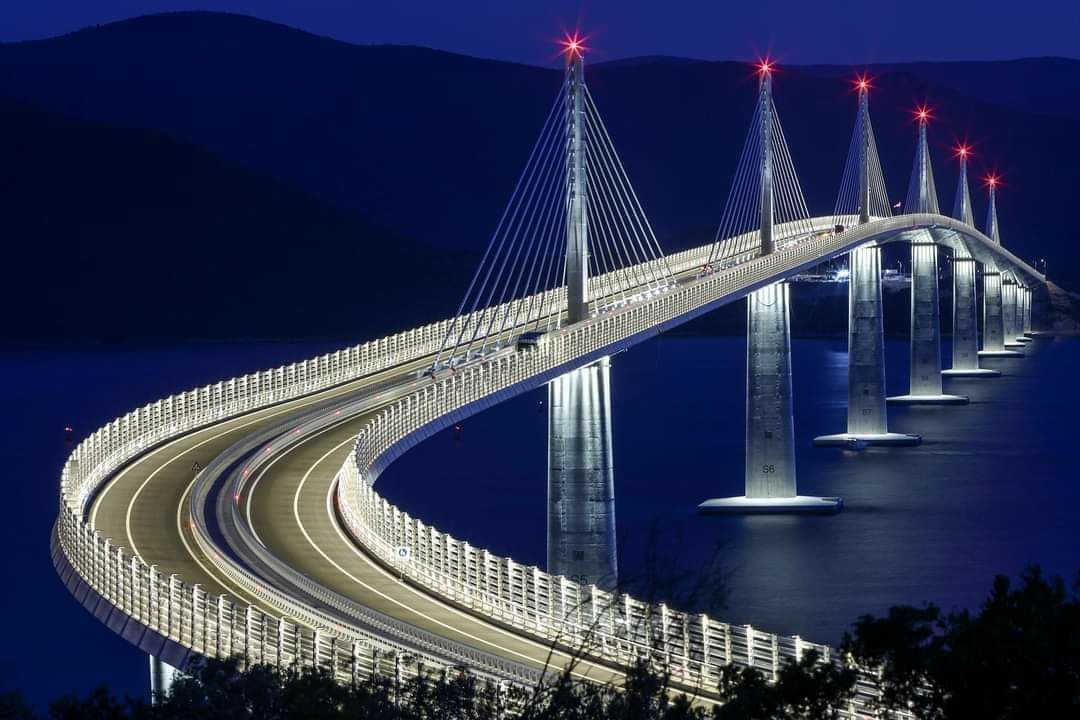
ln order to meet the main criteria of quality design, such as stability, durability, economy and integration into the environment, the design proposed the construction of an extra dosed bridge with an integrated hybrid structure. Structure is comprised of five central spans, each 285-m long, and six low pylons. Especially careful approach was taken to ensure durability for the extended lifespan of over 130 years. Cortec’s MCI® 2018 was specified on this project during the design phase as a silane-based impregnation with a migrating inhibitor property to protect against the harmful effects of corrosion, thus extending the service life of the bridge. MCI® 2018 is a 100% silane-based concrete sealer, containing migrating corrosion inhibitors that allow deep penetration into concrete and provides water repellence by chemically reacting with the cementitious substrate. It seals surface pores, preventing the intrusion of chlorides, reduces carbonation, and protects from the ingress of wind-driven rain. Treated concrete surfaces are fully breathable and their natural moisture-vapor transmission is not affected. After repair of surface damage and cleaning of discolorations and other surface defects, the concrete surface of the pylons needed to be protected with a colorless silane coating to improve durability and increase the resistance of the concrete surface to long-term external influences. MCI®-2018 carries CE certification that indicates conformity with health, safety and environmental protection standards for products sold within the European Economic Area (EEA).
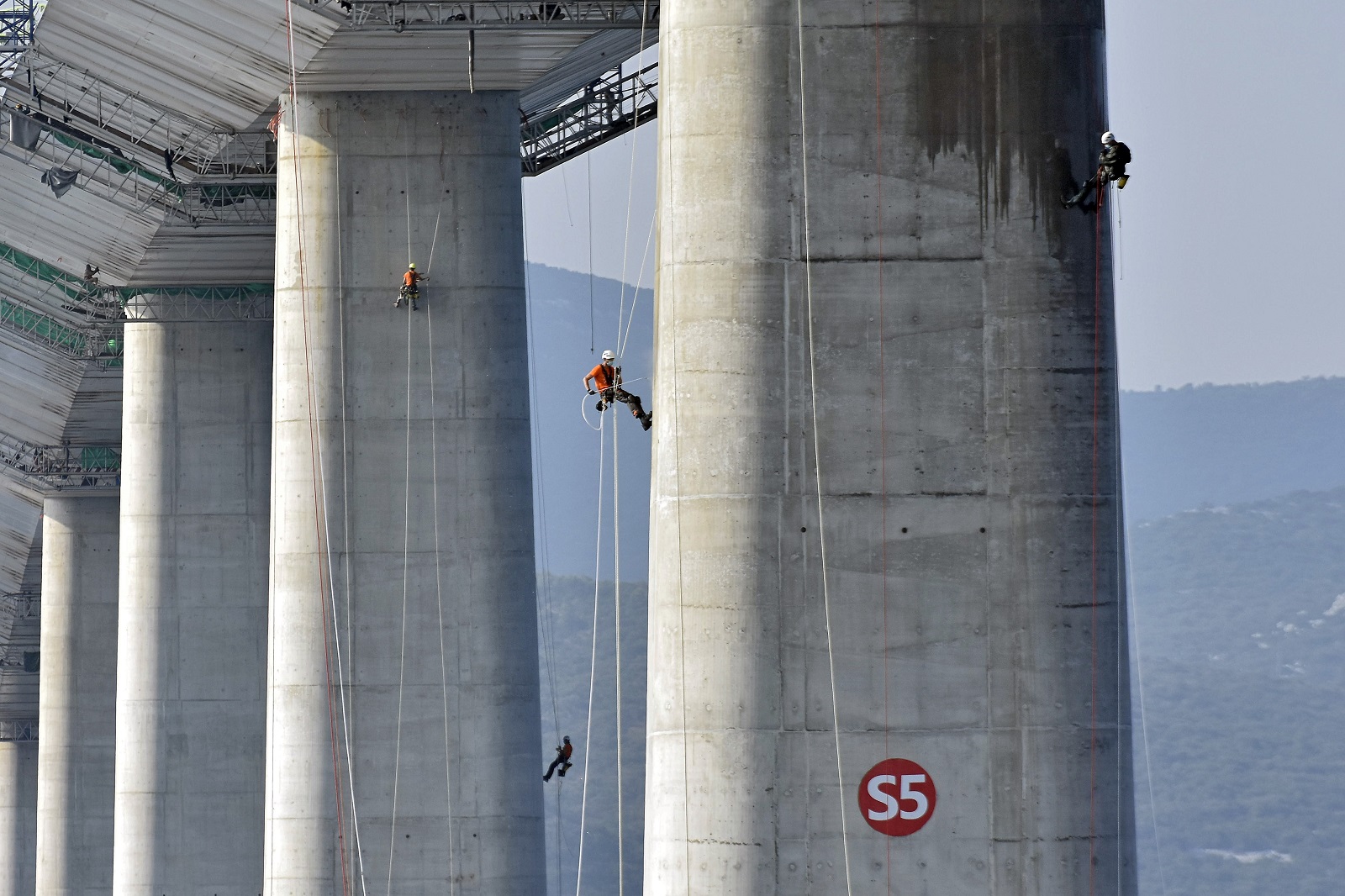
Application of Cortec’s MCI®-2018
A combination of AC coatings, cathodic protection of steel reinforcement in piles and pile heads, a concrete cover of 65–85 mm stainless steel reinforcement and impregnation of all concrete surfaces with MCI®-2018 was selected. This was chosen as the strategy to help the bridge achieve a 130-year service life. MCI®-2018 was applied on the entire substructure of the bridge. All concrete parts were coated with MCI®-2018 by a spraying technique. The work was performed in accordance with the project requirements and after surface preparation to full functionality.
This included:
- Access to pylons
- Rehabilitation of the concrete surface of the pylons
- Cleaning the concrete surface of the pylon (washing the pillars with water)
- Impregnation of the concrete surface of the pylon with MCI®-2018.
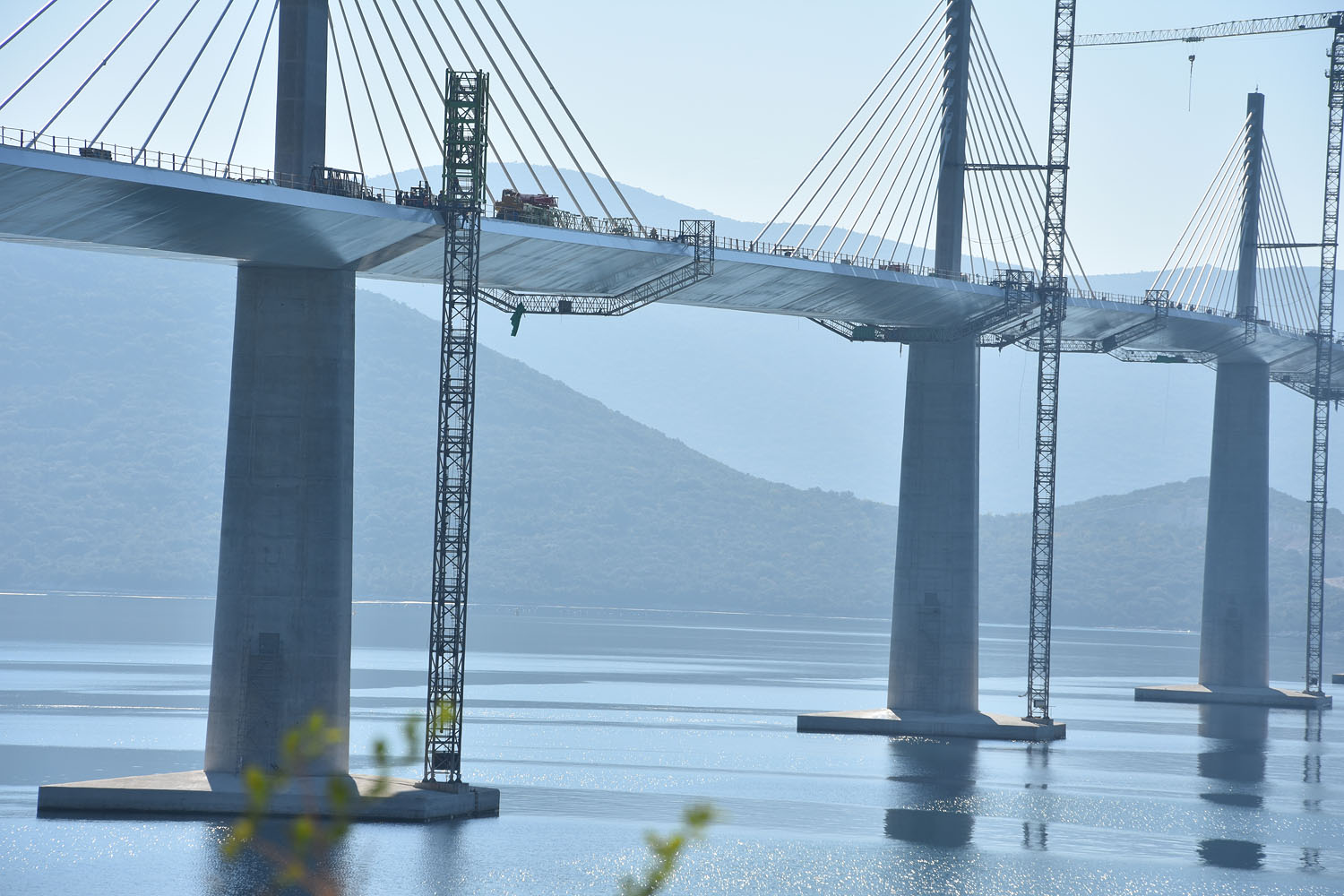
MCI®-2018 contains time-proven Migrating Corrosion Inhibitors (MCI®). The silane component provides water repellency by chemically reacting with the cementitious substrate under proper application, decreasing the ingress of aggressive materials. The product penetrates deep into concrete, providing corrosion protection to reinforcing steel from existing water and chloride ions, or other contaminants. Continuous monitoring of the condition of the structure at one central place was done during the construction phase and will be done at the exploitation phase to examine parameters of structural behavior, time, seismic activity, and structural durability. The designer of the bridge specified corrosion protection for all concrete segments in order to achieve a 130-year service life.
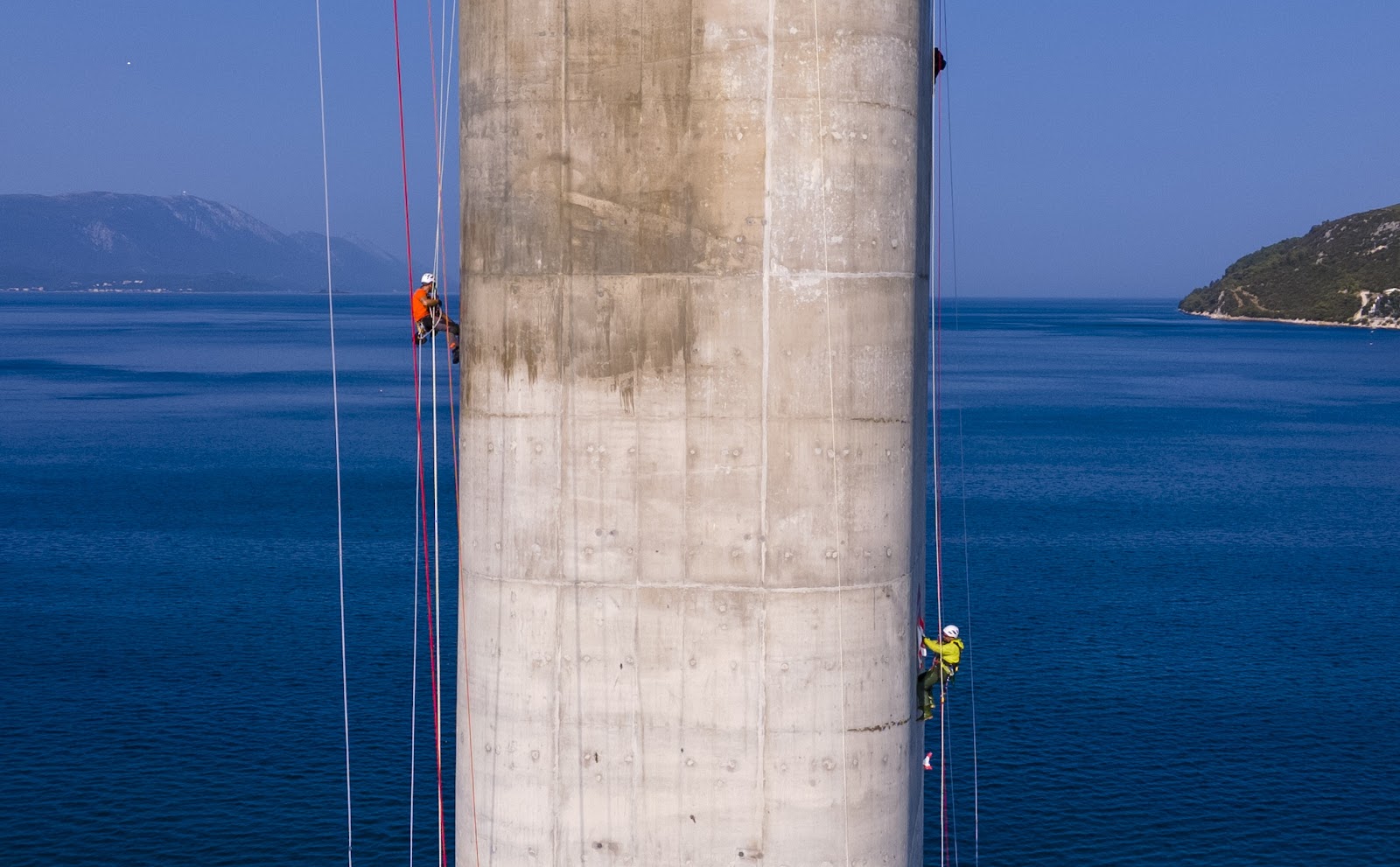
Cortec’s CEO, Boris Miksic, Croatian-American businessman is proud that his patented technology was used on this historic project to connect two parts of his country. “Our MCI® technology is used in largest construction projects throughout the globe. Witnessing its application in my home country on this monumental bridge structure is truly a special. Peljesac bridge is huge step forward for all of us.” A strategic investment such as this bridge, demonstrates European Commission’s commitment to bring people together and unite territories, while reinforcing the territorial cohesion of the region and helping other neighboring countries.