Reading Time: 5 minutes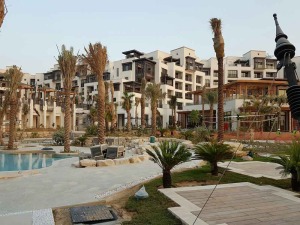
A view of the property’s exterior.
Innovative structural engineering was needed to ensure Dubai’s newest tourism hotspot, the Jumeirah Al Naseem, took full advantage of its spectacular location. Construction of the Jumeirah Al Naseem was announced in late 2012 by His Highness Sheikh Mohammed bin Rashid Al Maktoum, Vice-President and Prime Minister of the United Arab Emirates (UAE) and Ruler of Dubai. At the time, he emphasised how Dubai’s tourism infrastructure must match the UAE’s increasingly strong position as an international tourism hub. Global infrastructure and engineering advisory firm Aurecon rose to the design challenges, helping ensure the venue delivers a truly five-star experience for its guests.
The opening of the new 430-room Jumeirah Al Naseem gives substance to the Ruler of Dubai’s ambition. The fourth luxury hotel within the Madinat Jumeirah Resort development, the Jumeirah Al Naseem links with the three existing Jumeirah resorts, which occupy a prime spot on the stunning local coastline. The Resort, Dubai’s largest, was recently named in the Top 3 hotels of the Middle East and Africa by Travel + Leisure magazine.
Aurecon started work on the Jumeirah Al Naseem in December 2012 when the company was invited to collaborate on a range of engineering disciplines by leading development and management company, Mirage Leisure and Development. Aurecon and Mirage have collaborated on several previous developments within the Madinat Jumeirah Resort. Other companies appointed to the project included South African architects, Northpoint, who delivered the concept, and the Dubai office of Woods Bagot, who served as executive architect.
Having been awarded several engineering disciplines within the project, Aurecon began its design work in 2013. Civil and structural work was led by the local Dubai office with support from Aurecon’s office in Cape Town, while acoustics design, vertical transportation, marine design, waste management and geotechnical design was handled by experts in other global offices in Australia and South Africa.
Wouter Brand, Technical Director of Buildings and the Project Director for Aurecon’s work on the Jumeirah Al Naseem, says the company’s previous experience in the region, particularly in hotels and resorts, proved invaluable in making this project a success.
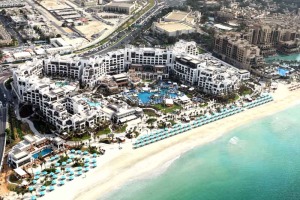
The opening of the new 430-room Jumeirah Al Naseem gives substance to the Ruler of Dubai’s ambition.
“Our knowledge of the local construction industry was as important as our ability to provide engineering solutions to the many design challenges of the project,” he said. “Creating a seamless connection with the rest of the resort was essential, as was making the most of its geographic location, lying across the water from the spectacular Burj Al Arab Jumeirah and delivering incredible sea views to all guest rooms.”
Challenging Designs
One of the biggest challenges to the structural design was to accommodate the complex building geometry and orientation of the hotel rooms, which were not compatible with the structural grid of the supporting basement car park. The lower level car park was designed with a rectangular grid of supporting concrete columns and walls for effective traffic flow and generous parking bay sizes. However, the structural column grid for the superstructure was restricted by the orientation of the hotel rooms and corridors, as well as the siting of the public entrances, retail and services spaces on the ground floor.
Adjusting the orientation of the hotel was not an option because every room was required to have a sea view; while the grand entrance hall was situated to give guests a sweeping vista of the iconic Burj Al Arab Jumeirah. With numerous balconies and floor plates that stepped back with increasing height, the combined design challenges made for an intricate and highly detailed engineering process.
“The optimal solution to this engineering challenge was the introduction of a concrete transfer slab to overcome the differences between the column grid above and below the ground level” said Faan Calitz, Technical Director of Structural Engineering at Aurecon. “The transfer slab system, which in certain areas is in excess of a metre thick, proved to be one of the challenging technical aspects of the project.”
The design had to ensure low deflection of the transfer slab and provide structural redundancy against earthquake loads. It was made more demanding because the transfer slab does not have a uniform thickness or a uniform top level, as it also has to support landscape, planting and pool areas, which lie at different levels around the ground floor of the hotel.
Geotechnical and Marine
Early involvement with the geotechnical and enabling works contractor was also crucial to the success of the project. Aurecon recommended the site be vibro-compacted to improve soil conditions and reduce the risk of liquefaction, which can occur during a seismic event. This compaction lowered the ground level by 400 mm and was an effective ground improvement solution.
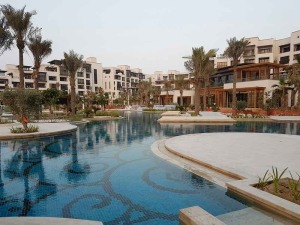
Aurecon started work on the Jumeirah Al Naseem in December 2012.
In addition, Aurecon carried out a Marine Study for the project, which assessed the vulnerability of the coastal development to severe storm surges. The study included a risk assessment of possible flooding and associated inundation and run-up levels, and care was taken to ensure that ground floor levels of the hotel were above possible flood levels. Aurecon also designed marine protection elements, which included sheet piling to the front of the property to prevent undermining of the structure.
Local Knowledge
As with all projects in Dubai, Aurecon’s design had to be approved by Government authorities before any construction could proceed. This approval process is aimed at ensuring the highest standards of design and construction quality are maintained in Dubai.
“Aurecon understands the importance of achieving an approved design within the available timeframe, because this is essential if a contractor is to commence construction on time,” said Ben Hawkes, Senior Structural Engineer who was based at the project site. “The Middle East is well-known for the scale and spectacular nature of its designs, as well as ambitious timeframes that are set for development. This all adds to the importance of ensuring that the execution of any project includes a robust plan for achieving authority approvals.”
“At Aurecon, we are committed to engineering solutions that suit the designs and dreams of our clients,” he concluded. “Although it’s only one part of the overall development, the location and guest experience of Jumeirah Al Naseem is crucial to ensuring Dubai’s Madinat Jumeirah Resort remains one of the world’s leading tourist destinations for many years to come.”