Hong Kong and Macau are Asia’s Most Expensive Construction Markets to Build in 2024
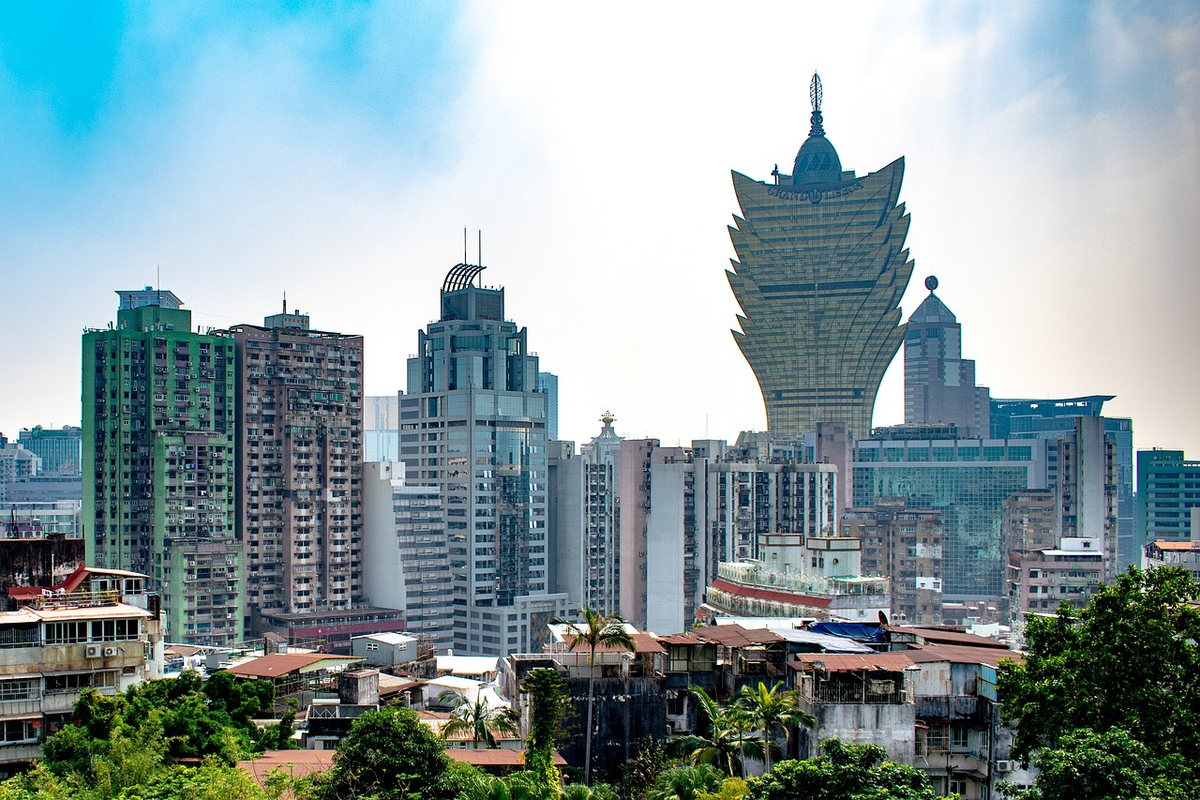
Hong Kong and Macau are Asia’s most expensive construction markets to build in this year at $4,500 and $4,269 per square metre respectively – and the ninth and 12th most expensive cities globally. The economic slowdown in China and the rise in nearshoring activities worldwide are opening up new construction opportunities for key emerging markets in Asia with Malaysia, Indonesia and India all benefitting.
The international trend of nearshoring, friend-shoring and reshoring is stimulating construction demand for local manufacturing bases in Asia to reduce reliance on cross-border trade. Meanwhile, as developed markets in the region adjust to both macroeconomic and domestic challenges, Hong Kong re-enters the top 10 list of most expensive markets to build in globally, in ninth place, with an average cost of US$4,500 per square metre, followed closely by Macau in 12th with an average cost of US$4,269 per square metre
The International Construction Market Survey (ICMS) 2024 report, from global professional services company Turner & Townsend, shows that while construction still faces challenges, inflationary pressure is softening, and stabilising costs are allowing investment flow in key global growth sectors such as data centres, healthcare and manufacturing.
From a survey of 91 global cities, except Hong Kong and Macau, all Chinese markets languish near the bottom of the overall cost table. China’s GDP growth is forecast to slow to 4.6 percent in 2024 from 5.2 percent last year1 as the country’s abundant labour force continues to keep costs low across its mainland markets.
Japanese cities, stalwarts in the top ten most expensive cities to build in globally for the past two years, have slipped out of the top rankings this year. Tokyo, ranked fifth, and Osaka, sixth, in 2023 are now the 13th and 17th most expensive markets to build in worldwide at US$ 4,127 per square metre and US$3,985 per square metre, respectively. Strong global inflation, moderate post-pandemic economic growth, and a significant devaluation of the Yen to a 34-year low, are key factors behind Japan’s lower overall construction costs this year. The weakened Yen, however, has spurred foreign investment into sectors such as data centres, advanced manufacturing and urban developments, all of which are experiencing high growth. Osaka, in particular, is seeing a major development boom as it prepares for World Expo 2025.
India has seen strong industrial investment as it strengthens its economic drivers – particularly in advanced manufacturing – as it looks to overtake China. This is seen in Bangalore, where advanced manufacturing construction costs are now US$1,861 per square metre, compared with US$568 per square metre in Shenzhen. Malaysia and Indonesia are also seeing high growth in manufacturing as part of this shift, and in Jakarta, the cost of advanced manufacturing construction has sharply risen.
A significant factor driving inflation worldwide is a scarcity of skilled labour. A staggering 79.1 percent of markets, representing 72 individual markets, reported skill shortages. This stands in stark contrast to just 9.9 percent, or 9 markets, with a labour surplus. The remaining 11 percent, or 10 markets, indicated a balanced labour market. This imbalance between supply and demand for skilled workers is putting continued upward pressure on construction costs globally.
Overall, the data points to lowering construction price inflationary pressure globally. Turner & Townsend has modestly reduced its 2024 construction cost inflation forecasts compared to last year. Construction cost inflation in most markets is driven by a backlog of projects, which are gradually moving forward as construction costs stabilise.
Sumit Mukherjee, head of real estate, Asia, at Turner & Townsend, said “In 2024 we’re seeing consistent trends across Asia in response to the impact of China’s economic slowdown. The shift to nearshore manufacturing, to neutralise the impact of China’s slowdown, is creating significant growth and opportunities as other Asian markets invest in sectors like advanced manufacturing. Other growth areas are being fuelled by Asia’s increasing population and wealth – with much greater demand for leisure and hospitality construction as well as investment in new education and healthcare facilities.
“In the context of this growth and opportunity – clients need to keep an eye on labour. Traditionally Asian labour markets are known for high availability and low wages – but as demand grows for specialist construction such as advanced manufacture and data centres, there may be bottlenecks of high-skilled workers in these sectors. Keeping close to supply chains and regularly assessing local development pipelines is essential to avoid potential issues.”