The Secret of MCI ® for Better Parking Ramp Maintenance
One of the biggest enemies of parking ramp longevity is corrosion. Whether a parking ramp is in a warm coastal area subject to sea breezes and salt spray or whether it is in the frozen north with cars tracking in deicing salts every winter, the basic story is the same. Chloride-induced corrosion leads to premature deterioration and early repairs on the reinforced concrete structure. To change this story, Cortec ® recommends adding Migrating Corrosion Inhibitors (MCI ® ) into routine maintenance to slow down the corrosion process.
Preventative Maintenance versus Repair
Preventing a problem is usually easier and less expensive in the long term than repairing a problem. When it comes to reinforced concrete parking ramps, corrosion prompts repair because it swells the size of the rebar, placing pressure on the concrete overlay and eventually causing it to crack and spall off. The farther this process goes, the more damage is done and the more material- and labour-intensive the repair. While adding corrosion protection to a repair is important to help it last longer, slowing down corrosion as part of routine maintenance is even better because it can delay and reduce damage.
MCI ® Surface Applied Corrosion Inhibitors (SACIs)
MCI ® SACIs are ideal for parking lot maintenance because they penetrate and migrate through concrete pores and can be combined with water repellents or traffic membranes. MCI ® molecules are attracted to reinforcing metal, where they adsorb and form a hydrophobic layer that inhibits the ability of the metal to interact with corrosives such as moisture and chlorides. This molecular barrier delays the time to corrosion initiation and slows down the rate of corrosion that has already started. MCI ® can be applied at any stage of a parking ramp’s life cycle – before, during, and after repairs.
Tips for Selecting the Right MCI ® SACI
Contractors and parking garage management companies can take a variety of paths when incorporating MCI ® into their preventative maintenance plan.
Those who want to aim for a 20-year MCI ® reapplication rate will typically want to choose MCI ® -2020 with a traffic membrane applied on top. Traffic membranes often have a 20-year warranty; however, when the membrane inevitably fails, it can allow water and chlorides to seep underneath and attack the concrete anyway. Applying MCI ® -2020 to the surface first will enhance protection by introducing the highest concentration of Migrating Corrosion Inhibitors of any SACI on the market.
For someone open to a corrosion-preventative maintenance period of seven to 10 years, MCI ® -2020 followed by MCI ® -2018 X is a good choice. This combination takes advantage of the highest concentration of surface-applied Migrating Corrosion Inhibitors topped by a 100% silane water repellent to keep MCI ® within and slow the ingress of corrosives.
For someone who wants to apply a two-in-one product, MCI ® -2019 or MCI ® -2018 are good options. MCI ® -2019 combines MCI ® with a 40% silane water repellent, making it ideal for tighter budgets. MCI ® -2018 combines MCI ® with a 100 percent silane water repellent for even better water repellency. These two SACIs are best applied in two coats, wet on wet, so there is no need to wait for dry time.
If a surface still has residual silane from a previous water-repellent application and it is not in the scope of the project to remove it, MCI ® -2019 can be used. This is because MCI ® -2020 and MCI ® -2018 may not penetrate a concrete surface that is partially covered with water repellents. However, MCI ® -2019 can be applied over residual silane water repellent with better penetration through the substrate.
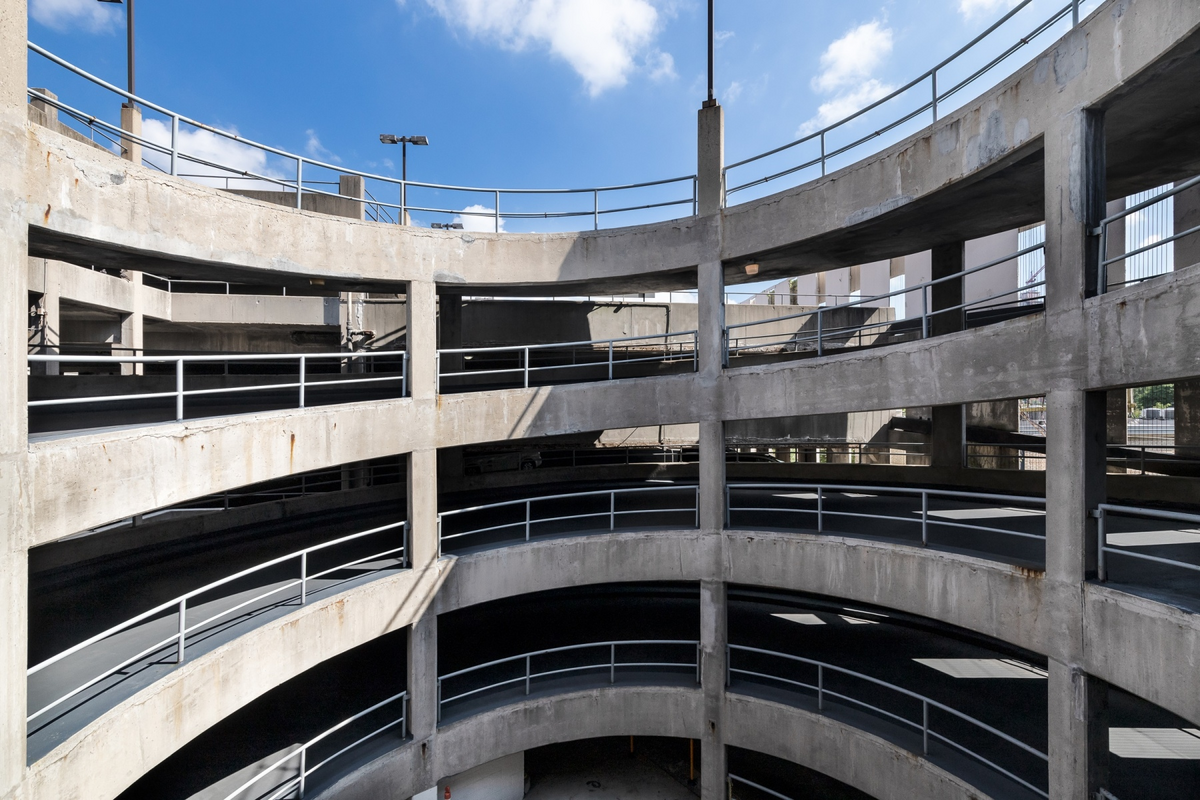
Start Your Preventative Maintenance Plan
Whatever a parking ramp’s age, it is not too early to start creating a corrosion-preventative maintenance strategy. Through the routine application of a water-repellent and Migrating Corrosion Inhibitor ™, parking ramp owners can push back the need for corrosion-related repairs and keep their parking structures in better condition longer to preserve property value.