Paving the digital path: Unpacking the impact of Singapore’s Budget 2024 on AI integration
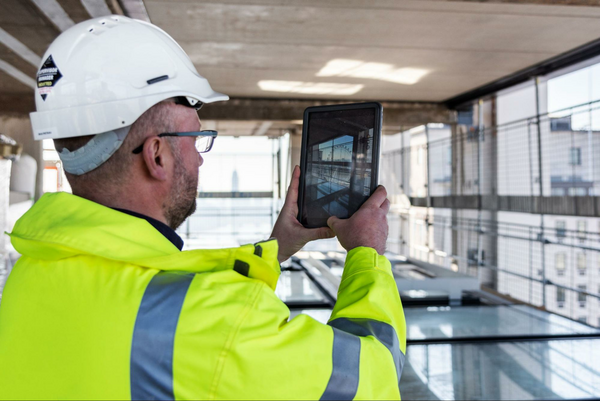
Singapore is forging ahead in AI and technology development, evident from the significant investments outlined in the recent Budget 2024 announcement. In the February Singapore Budget, substantial investments were unveiled to drive AI and technology initiatives. Over the next five years, the government aims to inject more than $1 billion into advancing multi-sector AI adoption, with a focus on nurturing talent and fostering industry growth.
Recognising AI’s transformative power emphasises the significance of human skill in the digital era. Moreover, Singapore is focusing on boosting its energy transition endeavours through a $5 billion investment. This move could alleviate financial constraints on clean energy initiatives, such as renewable energy generation and related infrastructure within industries like construction.
The focus on AI and technology presents a unique opportunity for the construction industry to undergo a significant transformation, and embracing these technological advancements will be essential for staying competitive in an increasingly digital landscape. AI-driven solutions are already allowing construction firms to optimise resource allocation, mitigate risks, ease bottlenecks, increase productivity and deliver projects more efficiently, ultimately driving greater value for stakeholders at all stages of a project’s lifecycle. At PlanRadar, we expect this trend of a digital-driven built environment to accelerate significantly in the coming months.
Closing the digital divide: How can companies sustainably adopt AI and smart building?
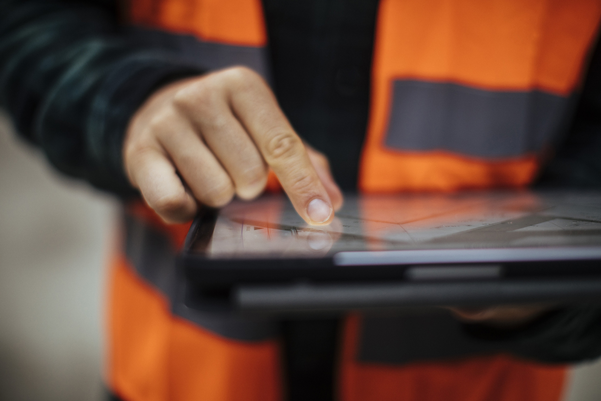
Bridging the digital divide necessitates a comprehensive strategy focusing on the accessibility and affordability of advanced digital tools. A promising approach involves offering tailored assistance and resources to smaller businesses in rural regions or developing nations, such as subsidised access to digital tools and extensive training initiatives to bolster technical skills in the workforce. By investing in educational and upskilling schemes, employees can gain the necessary technical prowess to effectively leverage smart technology.
The incorporation of AI and technology in any capacity should always enhance, not diminish, the role of human workers in the construction sector. PlanRadar understands that while machines excel at routine tasks and data handling, humans bring critical thinking, adaptability, and hands-on trade experience to the forefront. Additionally, human workers are essential for executive decision-making. Although automation and digital tools can streamline operations, it is crucial to leverage human creativity, expertise, and intuition for intricate problem-solving and decision-making processes. Through investment in training and upskilling initiatives, we can equip workers with the necessary digital literacy and technical skills to excel in an increasingly technology-driven landscape. This approach ensures that technology supplements, rather than replaces human capabilities.
By directly tackling these discrepancies, we can establish a fairer environment for digital integration within the construction sector across the ASEAN region.
Successfully integrating technology: Key ways to maximise industry incentives and funding
To maximise potential for government incentives and grants towards successful AI and digital technology adoption, construction companies in Singapore should consider the following strategies:
- Stay informed: Regularly monitor updates and announcements from government agencies such as the Building and Construction Authority (BCA) and Enterprise Singapore to stay informed about available incentives and grants.
- Alignment with government priorities: Align AI and digital technology adoption initiatives with the government’s priorities and strategic plans for the construction sector. This ensures that the company’s efforts are in line with national objectives, making it more likely to qualify for incentives and grants.
- Participation in government programs: Actively participate in government-led programs and initiatives aimed at promoting AI and digital technology adoption in the construction industry. This could include joining pilot projects, industry collaborations, or innovation challenges organised by government agencies.
- Collaborate with research institutions: Collaborate with research institutions, universities, or technology providers to develop innovative AI and digital solutions tailored to the needs of the construction industry. Government agencies often support collaborative research and development projects through funding and grants.
- Invest in employee training and skills development: Invest in training and upskilling employees to ensure they have the necessary knowledge and skills to effectively implement and utilise AI and digital technologies in construction projects. Some government incentives may prioritise companies that demonstrate a commitment to workforce development.
- Compliance and regulations: Ensure compliance with relevant regulations and standards related to AI and digital technology adoption in the construction sector. Companies that adhere to industry best practices and regulatory requirements are more likely to qualify for government incentives and grants.
By adopting these strategies, construction companies in Singapore can maximise their potential for government incentives and grants towards successful AI and digital technology adoption, thereby driving innovation and competitiveness in the industry.
The impact of the Singapore Budget 2024 on technology in the construction industry
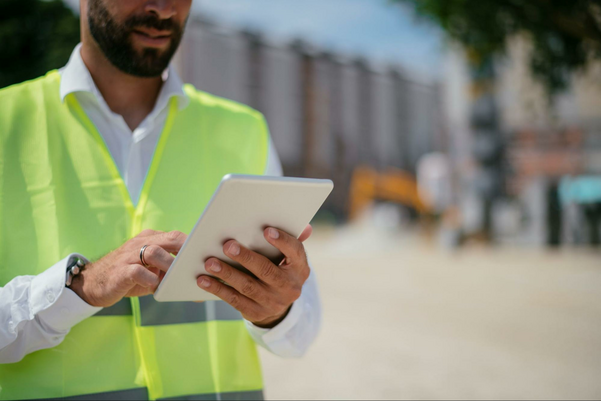
We expect that the 2024 budget will likely prioritise the role of technology in construction as part of Singapore’s broader strategy to maintain global competitiveness. With grants available to support AI technology adoption across all sectors, including construction, there is an anticipation of a concentrated effort to encourage companies to embrace digital innovation. This could involve specific initiatives aimed at fostering the use of AI, IoT, and smart technology in construction projects, along with investments in digital infrastructure and workforce development.
At PlanRadar, we foresee that construction firms stand to gain significantly from the available grants for acquiring AI technology. These funding opportunities offer companies a chance to invest in state-of-the-art AI solutions that boost productivity, enhance safety protocols, and streamline operations for construction projects of any size or complexity.
By leveraging the growing global significance and potential of AI, construction firms in Singapore can improve resource management, mitigate risks, and increase operational efficiency and profitability. We trust that these grants will inspire companies to embrace AI advancements, accelerate their digital transformation, and push for a competitive edge in a dynamic market environment.
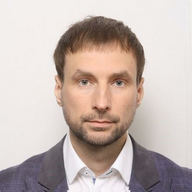
Vitaly Berezka is Head of Sales across Central Asia, MENA and APAC for the construction and real estate software company PlanRadar.
With an engineering degree in construction, Vitaly also holds an executive degree in business administration. His experience in the real estate development and construction industry spans more
than 15 years. Since 2013, he has held management positions in international companies that provide innovative solutions to the construction and real estate industries.
Besides lecturing on digitalisation topics at universities, he is the author of scientific publications and the co-author of three books. Vitaly is a member of International Real Estate Federation (FIABCI).