Reading Time: 3 minutesNew facility created to help printing companies and brands in Asia Pacific and Japan to bring their ideas to life
SINGAPORE — HP today announced the opening of a new Centre of Excellence (CoE) and the expansion of an HP Indigo ink manufacturing facility in Singapore. The facility aims to educate and inspire printing companies and their customers – including brands, agencies and print buyers – in Asia Pacific and Japan about new opportunities made possible by HP digital printing solutions.
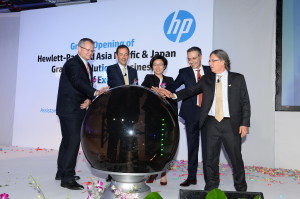
HP Executives and Guest of Honor, Thien Kwee Eng, Assistant Managing Director of the
Singapore Economic Development Board, at the opening ceremony for the HP Graphics Solutions Centre of Excellence and new Indigo Ink Manufacturing facility
The new 21,000 square metre facility will provide customers with one-stop access to HP’s broad digital printing portfolio and solutions, as well as a space to connect with experts and share creative and technical best practices.
The new facility will further support worldwide Indigo ink volume production by expanding local capabilities from the current ink series to the fast-growing new generation of inks for the HP Indigo 10000, 20000 and 30000 Digital Presses.
“Brand owners are facing increased competition as consumer choice and expectations have exploded. As a result, they’ve moved into the digital world to connect more powerfully with their customers,” said Gido van Praag, vice president, Graphics Solutions Business, HP Asia Pacific and Japan. “The new HP Centre of Excellence aims to give them the tools to compete, helping brands identify new ways to combine their unique skills with the industry’s broadest portfolio of innovative digital printing solutions, and its unparalleled application capabilities.”
The new facility will create employment opportunities in Singapore with more than 100 employees projected to be added to the facility in the next five years, most of which will include technical professionals and training personnel.
“We welcome HP’s latest investment as yet another milestone in the 44-year Singapore-HP partnership,” said Thien Kwee Eng, assistant managing director of the Singapore Economic Development Board. “Printing is an important industry, and the new HP Graphics Solutions Centre of Excellence and second Indigo ink manufacturing plant will help to transform the industry to capture opportunities from the growth of digital printing.”
HP Graphics Solutions Centre of Excellence Unlocks the Full Power of Digital Printing
The complete graphics portfolio and partner solutions along with an extensive gallery of applications – from stamps to building wraps – are housed in the new facility to make it easier for customers to unlock the full power of digital printing.
Printing companies will be able to benchmark and conduct end-to-end application testing of their HP digital printing equipment. Brands and agencies will be able to see inspirational ideas and work on pilot projects in a real-world production environment.
In addition, a training centre will help increase operator proficiency and expedite return on investment of HP Indigo Digital Presses, HP Scitex Industrial Presses, HP Latex and HP Designjet Printers. The centre, staffed by 11 training and ramp-up specialists, will provide hands-on learning and train more than 350 operators, engineers and production managers each year.
HP Ink Manufacturing Facility to Answer Fast Growth of New Generation HP Indigo Digital Presses
The increase in ink manufacturing capabilities supports the growing demand of Indigo next-generation presses, which are reaching 150 installations worldwide. These installations are in addition to more than 6,000 HP Indigo Presses now in 120 countries.
The 10,000 square metre expansion to the ink manufacturing plant will support global production of specialized HP Indigo ElectroInks for the new generation of HP Indigo 10000, 20000 and 30000 Digital Presses. The Indigo 10000, the first B2-format digital press with offset quality, enables print service providers, photo specialty shops and book printers to provide high value, high productivity applications. The Indigo 20000 and the Indigo 30000 Digital Presses, released to the market earlier this year, are the first digital presses designed to meet the needs of label & flexible packaging and folding carton converters.
To allow HP Indigo customers in the region to order and receive more than 3,000 specially mixed ink colours within short lead times, the plant will also manufacture Pantone®-licensed spot colour inks.
Substrate testing and certification capabilities will be built into the plant to enable substrate manufacturers, suppliers and HP Indigo press owners from Asia Pacific and Japan and Europe, the Middle East and Africa to evaluate substrate compatibility with HP Indigo Digital Presses.
The new ink manufacturing facility is scheduled to open in 2015.
Additional information about HP Indigo digital printing is available at hp.com/go/indigo, on the HP Graphic Arts YouTube channel, youtube.com/HPGraphicArts, or through the HP Graphic Arts Twitter Feed, twitter.com/hpgraphicarts.